Rail Car
Services
Custom On-Site Services and Program Development
Railcar Repair
The United States Federal Railroad Administration (FRA) allows the use of 8 NDT methods (AE, LT, MT, PT, RT, UT, IR, or VT/RVT) to inspect in-service railroad tank cars with fusion welds. These 8 NDT methods replaced hydrostatic testing years ago. The inspections help evaluate high-stress areas, including welds, on the bottom of the tank and may be used to qualify tank cars for a 10-year inspection cycle. Facilities performing railcar repair and inspections should comply with the following:
- Nondestructive testing personnel must be qualified and certified in accordance with the Association of American Railroads (AAR) Manual of Standards and Recommended Practices (MSRP) M-1002, Section C Part III Appendix T. This standard establishes personnel training hours, NDT procedure requirements, and inspection reporting requirements. Companies must have a written practice describing the program for the control and administration of NDT personnel training, examination, and certification modeled on AAR Appendix T and ASNT SNT-TC-1A. The program should be approved and administered by an NDT Level 3.
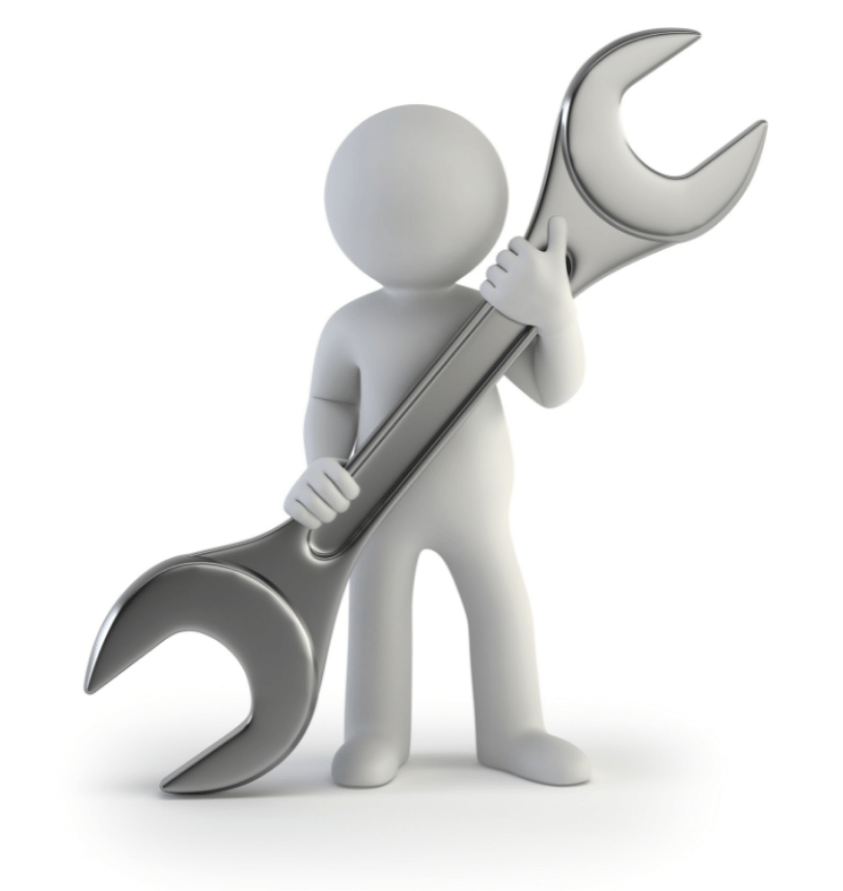
- Typical inspection areas for qualifying tank cars are as follows:Visual inspection of the interior and exterior of the tank. These inspections include inspection of tank welds, shells and heads for abrasion, corrosion, cracks, dents, distortions, weld defects, or any other condition that would make the tank unsafe for transportation.
- Structural integrity inspection using one or a combination of 6 methods Liquid Penetrant (PT), Magnetic Particle (MT), Radiographic Testing (RT), Ultrasonic Testing (UT), Direct and/or Remote Visual Testing (VT/RVT), and Acoustic Emission (AE). The inspection involves a structural integrity inspection of all transverse fillet welds and termination of longitudinal fillet welds greater than 0.25 inches (0.64 cm) within 4 feet (121.92 cm) of the bottom longitudinal centerline of the tank car. The structural integrity inspection also includes an inspection of tank shell butt welds within 2 feet (60.96 cm) of the bottom centerline that have structural discontinuities and/or terminations of reinforcements within 12 inches (30.48 cm) of the weld.
- Thickness check of the tank shell, heads, sumps, domes, and nozzles. The minimum allowable thickness should be mandated and will vary with car design. This check may not be required for tank cars that have a lining/coating program.
- Safety system inspection on all safety equipment (e.g., thermal protection, safety relief devices, and nozzle protection systems) to verify functionality and presence.
- Lining and coating inspection. A general inspection of interior coatings and linings, if applicable, are in proper conditions.
- A leak test of service equipment (e.g., tank, service equipment, and closures) is performed to ensure they are leak-free.
- Typical inspection areas for qualifying tank cars are as follows:Visual inspection of the interior and exterior of the tank. These inspections include inspection of tank welds, shells and heads for abrasion, corrosion, cracks, dents, distortions, weld defects, or any other condition that would make the tank unsafe for transportation.
Probability of detection (POD) studies have been funded by the FRA. One of such studies, completed in April 2021, titled “Analysis of Historical Non-Destructive Evaluation Probability of Detection Data for Railroad Tank Cars,” demonstrated that a group of inspectors with various levels of experience and certifications performing inspections using CFR-approved NDT methods were not capable of achieving or approaching a 90-percent probability of detection (POD) with 95-percent confidence (90/95 POD) for fatigue cracks in butt weld test panels. Evaluation of the fillet weld data showed mixed results, but only the magnetic particle testing (MT) method reached 90/95 POD. A portion of their summary is stated below:
“Researchers strongly recommend a refresher training course especially if an inspector is new to a company. All inspectors should be trained and capable to detect both manufacturing defects and fatigue related cracks, not just one or the other. The NDT research team’s observations during these inspections, and evaluations of results using DOEPOD, detected significant variations in training procedures for inspectors among the industry. Researchers recommend that adequate specialized training on all CFR-approved NDE methods is necessary for personnel inspecting tank cars, regardless of the manufacturing or revenue service location. Also, the DOEPOD analysis determined that a more thorough calibration step should be followed and written into the procedure for each company. This includes performing a calibration using the type of material being inspected instead of calibration blocks.“
How would your inspectors perform in a POD study? Premier NDT Resources can be a great resource and partner in updating, modifying, or maintaining your NDT program locally and nationally. We can bolster any inspection program with custom training and procedures to fill potential knowledge gaps.
When it comes to your Railcar NDT needs, don’t count on just anyone with NDT certifications. The experts at Premier NDT Resources have real-life experience in developing, implementing, applying, and applying compliance to the NDT industry’s most stringent standards. We are customer-minded and focus on compliance, safety, and effectiveness. Our team is friendly, adaptable, and able to work with people at all levels. Whether developing a turn-key program, performing technical performance evaluations, or writing and qualifying procedures, we’ve got your back.
Development
Auditing
Services
Services
Development
NDT Program Development and Administration
Railcar Nondestructive Testing Program Development
- Provide Level 3 oversight
- Develop, review and approve Written Practices
- Develop, implement, and maintain NDT Program in part or as a whole
- Develop, qualify and approve NDT procedures and techniques
- Perform technical performance evaluations
- Maintain overall control and cognizance over the NDT training program
- Develop, administer, review, and approve NDT training
- Develop, administer and grade general, specific, practical, and visual acuity exams required for certification
- Verify qualifications of candidates and recommend them for certification
- Evaluate and document the technical performance of NDT technicians
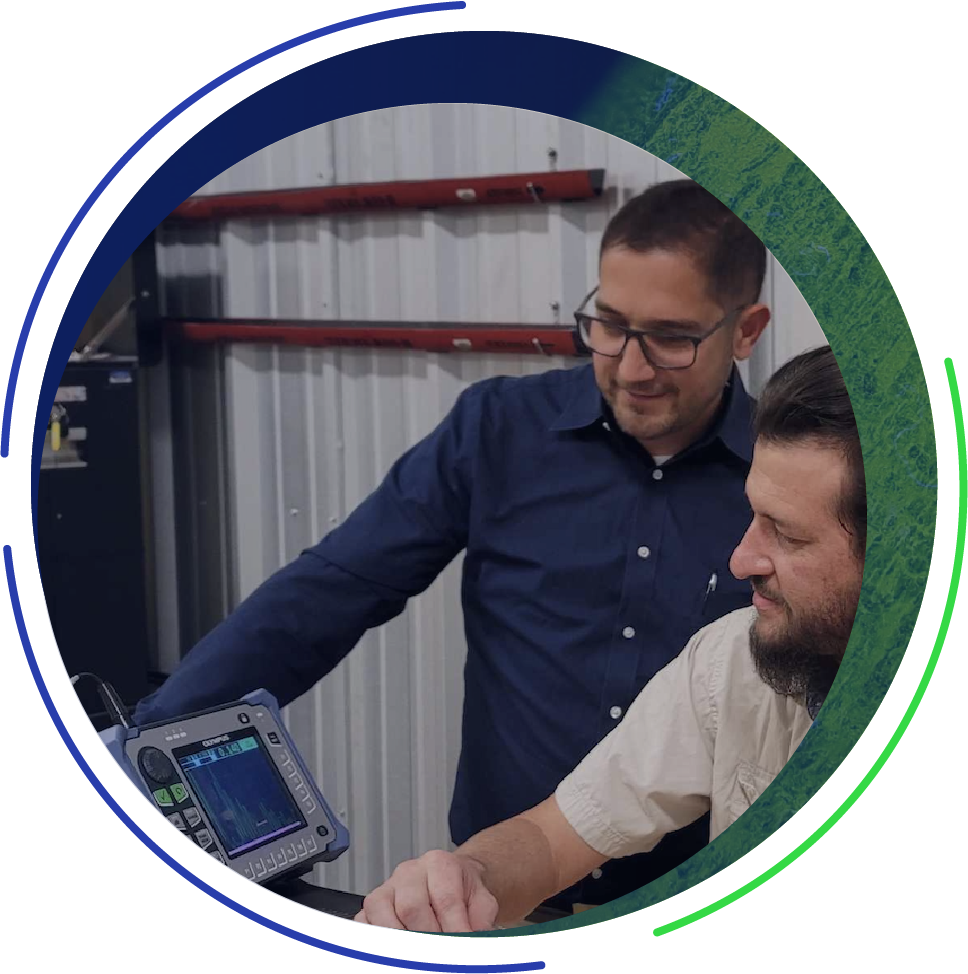
Auditing
PROGRAM AUDITING
Railcar Program Auditing
- Perform internal company audits on the quality system, NDT, welding, or ITAR programs
- Perform program gap assessments
- Perform pre-audits in preparation for an external audit
- Develop audit checklists
- Audit personnel and processes for compliance and efficiency
- Represent the company during external audits
- Provide suggestions for program/system improvement
- Provide an outside view on system completeness, effectiveness, and applicability
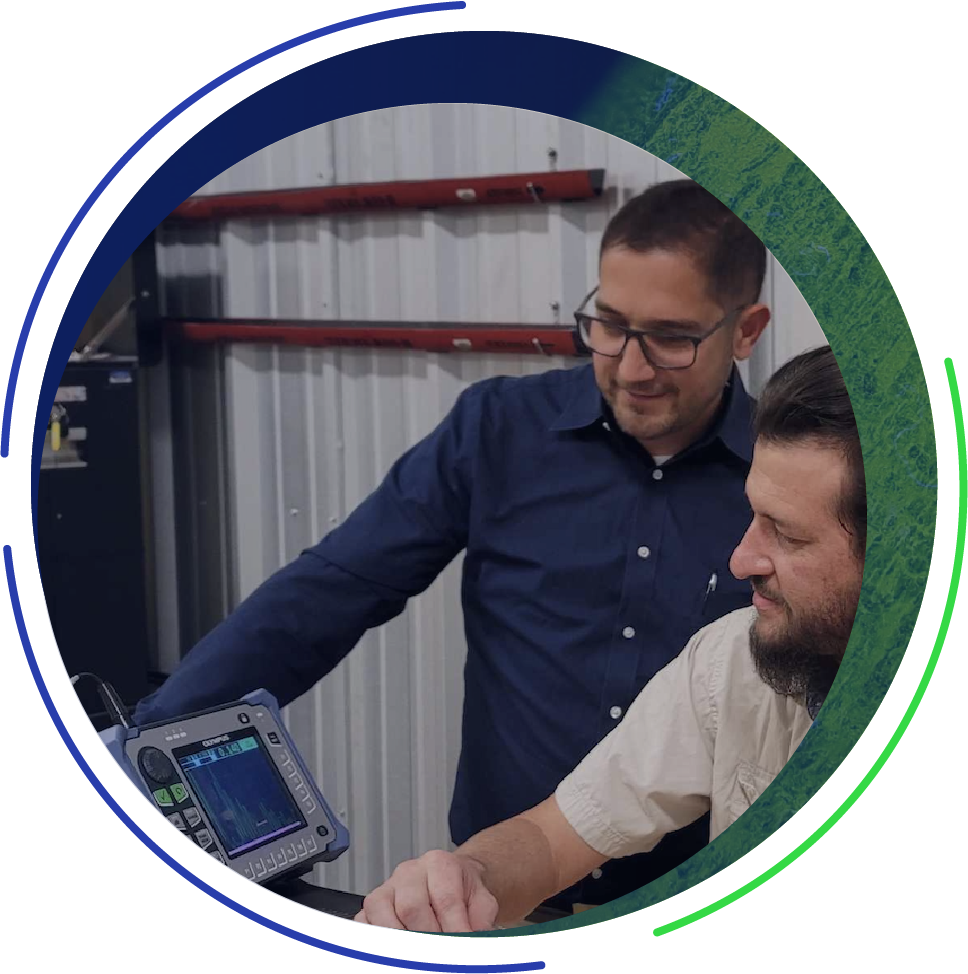
Services
NDT LEVEL 3 SERVICES
Railcar Nondestructive Testing Level 3 Services
- Reviewing new revisions of codes, specifications, recommended practices, etc. and updating company procedures accordingly
- Interpret codes, specifications, standards and procedures and designate NDT methods to be used
- Interpretation and evaluation of results in terms of existing codes, standards, specifications, etc.
- Implement corrective actions from internal or external audits
- Develop or evaluate new or existing inspection techniques
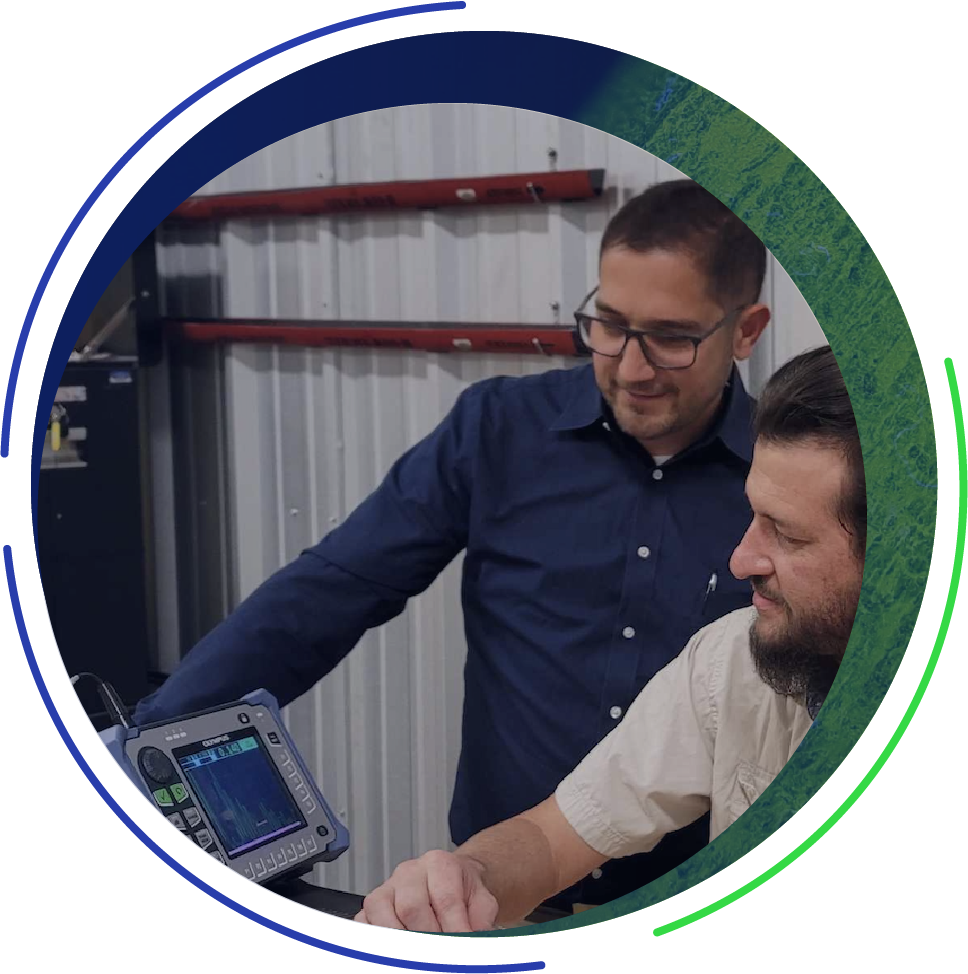
Services
TRAINING SERVICES
Railcar Nondestructive Testing Training
- Administer AAR MSRP M-1002, Section C Part III Appendix T and SNT-TC-1A compliant NDT training for VT, PT, MT, UT, RT, and ET
- Develop, administer and grade general, specific, practical and visual acuity exams required for certification
- Administer railcar specific classes such as UT Weld Inspection, Advanced Characterization and Sizing of Flaws with UT, etc.
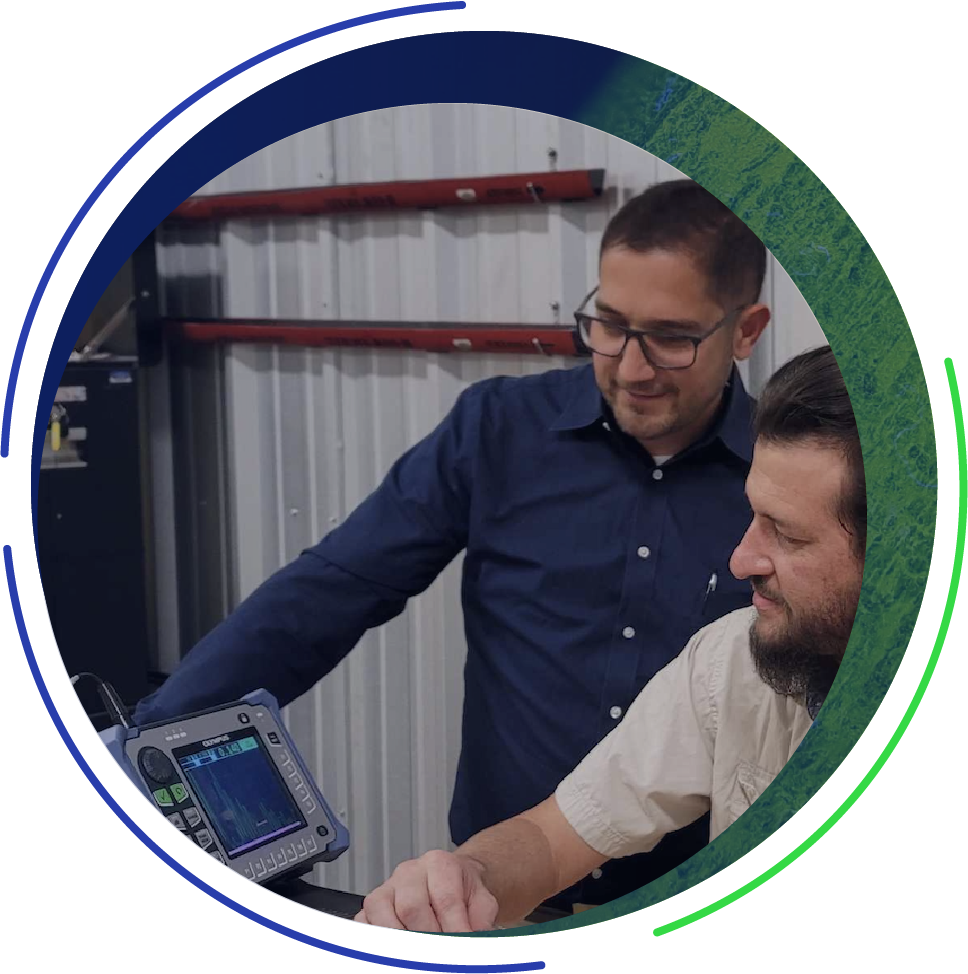
NDT Program Development and Administration
Railcar Nondestructive Testing Program Development
- Provide Level 3 oversight
- Develop, review and approve Written Practices
- Develop, implement, and maintain NDT Program in part or as a whole
- Develop, qualify and approve NDT procedures and techniques
- Perform technical performance evaluations
- Maintain overall control and cognizance over the NDT training program
- Develop, administer, review, and approve NDT training
- Develop, administer and grade general, specific, practical, and visual acuity exams required for certification
- Verify qualifications of candidates and recommend them for certification
- Evaluate and document the technical performance of NDT technicians
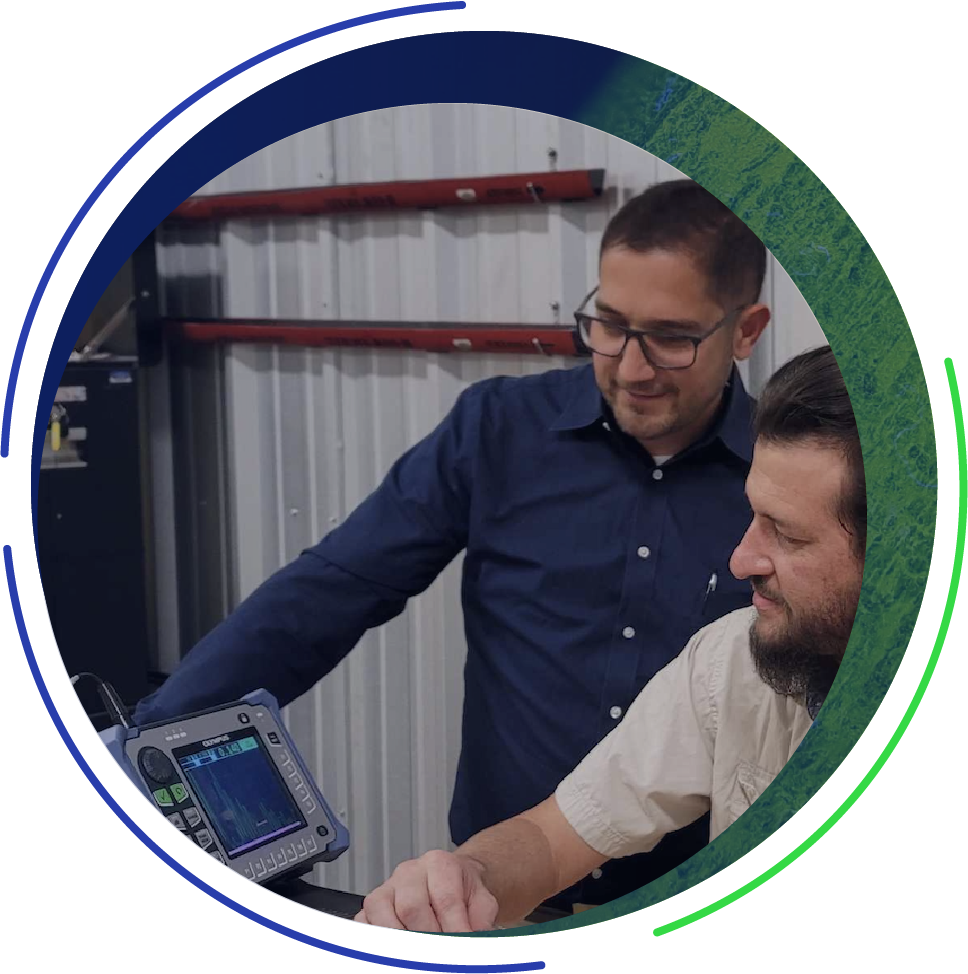
PROGRAM AUDITING
Railcar Program Auditing
- Perform internal company audits on the quality system, NDT, welding, or ITAR programs
- Perform program gap assessments
- Perform pre-audits in preparation for an external audit
- Develop audit checklists
- Audit personnel and processes for compliance and efficiency
- Represent the company during external audits
- Provide suggestions for program/system improvement
- Provide an outside view on system completeness, effectiveness, and applicability
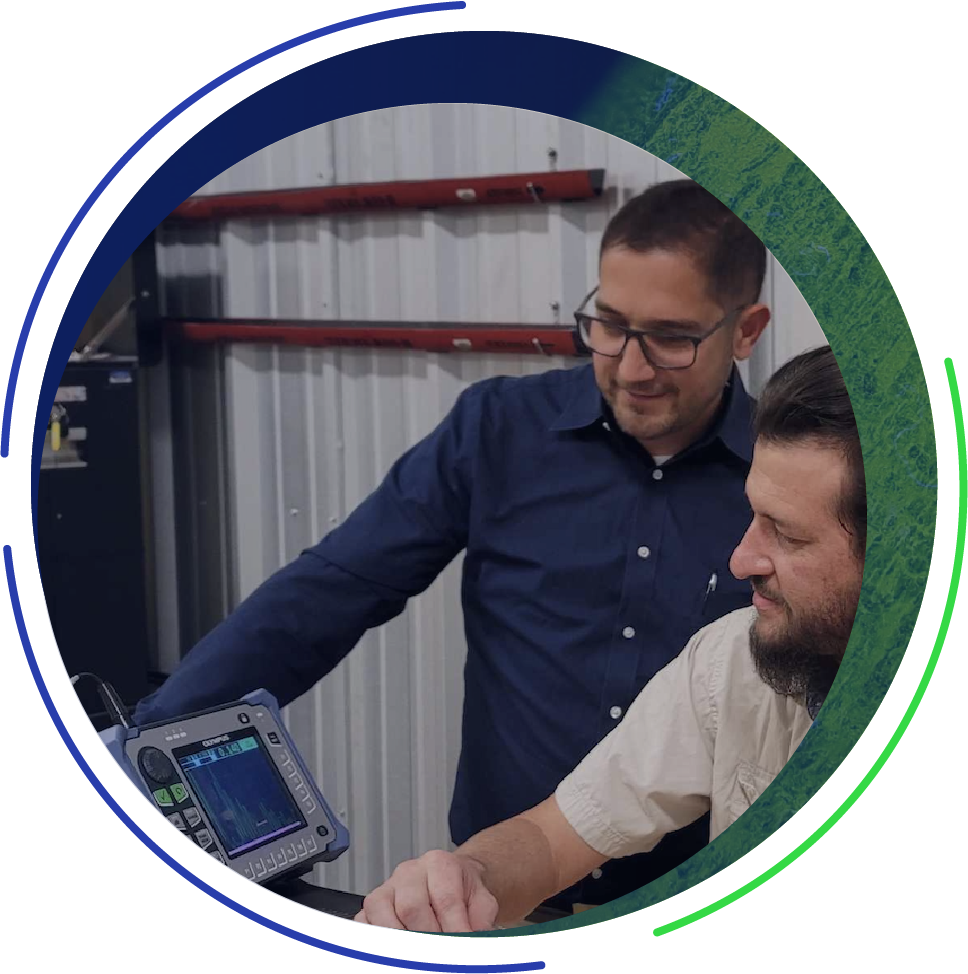
NDT LEVEL 3 SERVICES
Railcar Nondestructive Testing Level 3 Services
- Reviewing new revisions of codes, specifications, recommended practices, etc. and updating company procedures accordingly
- Interpret codes, specifications, standards and procedures and designate NDT methods to be used
- Interpretation and evaluation of results in terms of existing codes, standards, specifications, etc.
- Implement corrective actions from internal or external audits
- Develop or evaluate new or existing inspection techniques
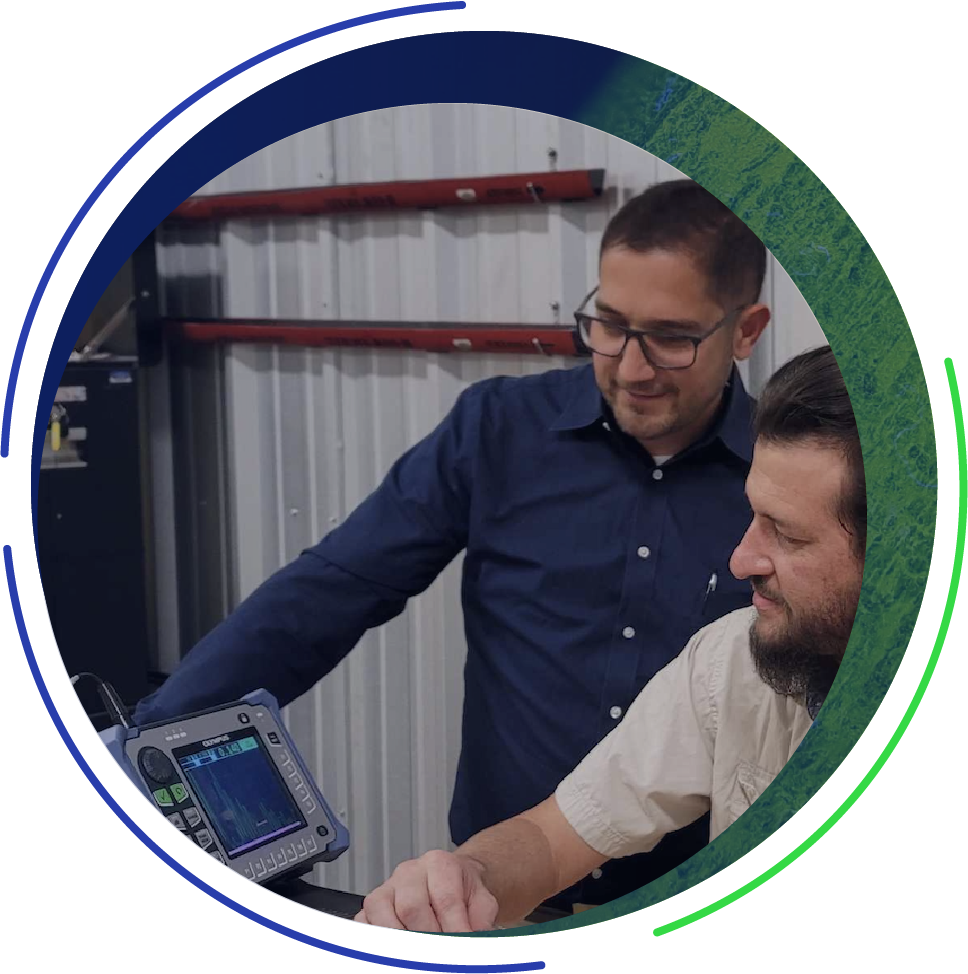
TRAINING SERVICES
Railcar Nondestructive Testing Training
- Administer AAR MSRP M-1002, Section C Part III Appendix T and SNT-TC-1A compliant NDT training for VT, PT, MT, UT, RT, and ET
- Develop, administer and grade general, specific, practical and visual acuity exams required for certification
- Administer railcar specific classes such as UT Weld Inspection, Advanced Characterization and Sizing of Flaws with UT, etc.
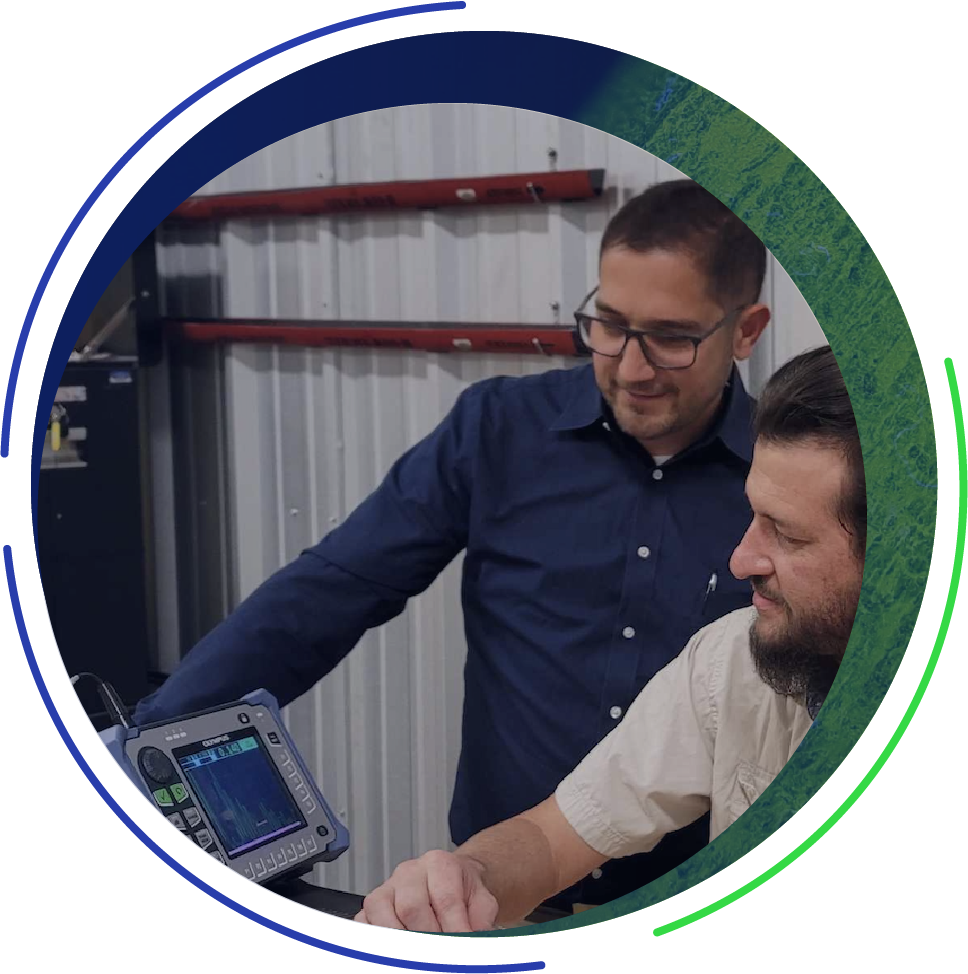
Premier NDT RESOURCES Dedicated Service TeaM
Our team will respond within 24-hours